Predictive Maintenance vs Preventive Maintenance: Choosing The Best One
Published on: 9th December, 2024
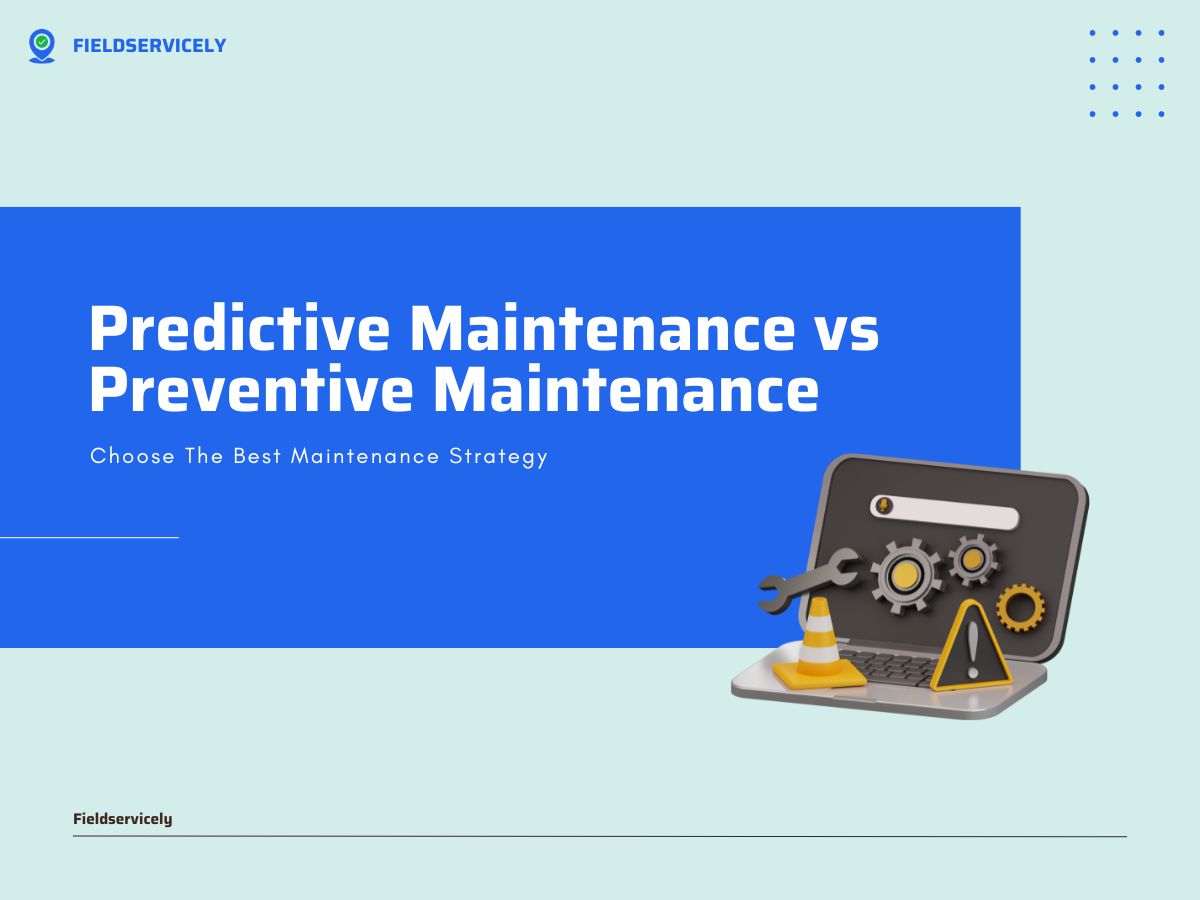
Predictive maintenance vs preventive maintenance has been a common debate for businesses looking to optimize their maintenance strategies. Especially after the Industry 4.0 revolution.
- Around the world, 47% of manufacturing companies rely on predictive maintenance (PdM).
- Predictive maintenance have the ability to cut machine downtime by 30%-50%. Also, can maximize machine lifespan by 20%-40%.
- Over 80% (according to some sources, 88% before 2021) of global manufacturing companies still continuing preventive maintenance (PM) along with PdM strategies.
- According to ABI Research, PdM topped PM in AI-enabled devices and workflows, with an expected installed base of 9.8 million in the next five years.
This provides a foundational understanding of predictive vs preventive maintenance. Go through the whole article to learn more about which approach is best suited for you.
See till the end of the debate to find out which one is best. Also, explore to find out about other maintenance type and their performance. For instance, reactive vs preventive maintenance vs predictive maintenance or– corrective maintenance.
Predictive Maintenance
This is the most appreciated maintenance type in the last decade. Predictive maintenance (PdM) has grown fast. With the integration of Big Data, better connectivity, automation, and other tools of Industry 4.0 it has become stronger in reducing cost, time, and labor.
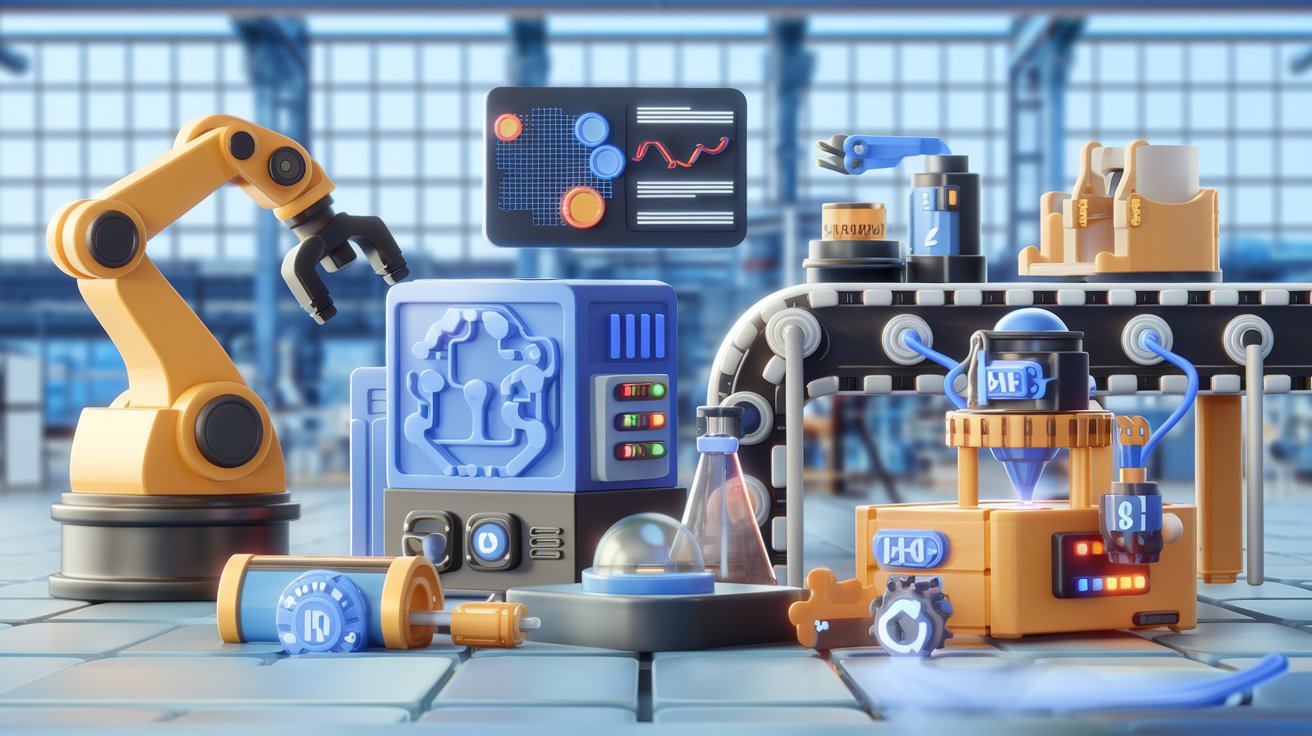
Even McKinsey Global Institute reported last year that with the implementation of PdM, manufacturing companies worldwide can save around $240bn-$627bn in expenses.
Meaning and Definition
In short, predictive maintenance (PdM) refers to forecasting machine failure and following that required maintenance. It’s not a condition-based maintenance type like any other.
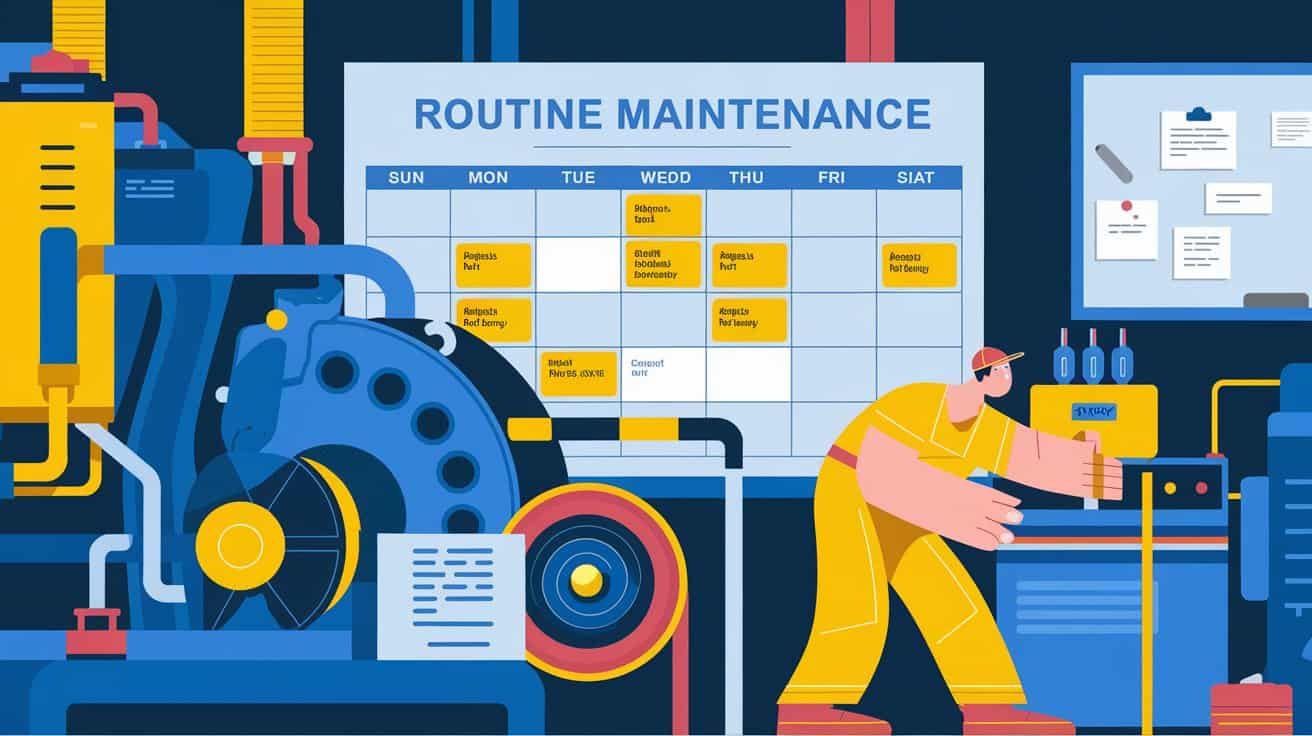
Rather it’s an anticipation type maintenance. PdM is a proactive maintenance strategy that leverages advanced technologies and data analytics to anticipate when equipment is likely to fail or require maintenance.
Data plays a huge role in PdM. By analyzing real-time data and historical performance, PdM helps companies address potential issues before they lead to significant problems or downtime.
So the results depend quite on the quality and quantity of data. The higher the quantity, the higher chance to get a pattern and forecast accordingly. High-quality data ensures precise predictions and reliable maintenance schedules.
Preventive Maintenance
One of the first modern-day maintenance types that brought a great change. Preventive maintenance (PM) was first termed by H.P. Fairman in 1909 to classify the reasons for energy loss. But it was in 1914 when the maintenance type was sealed with a publication and became popular among various industries.
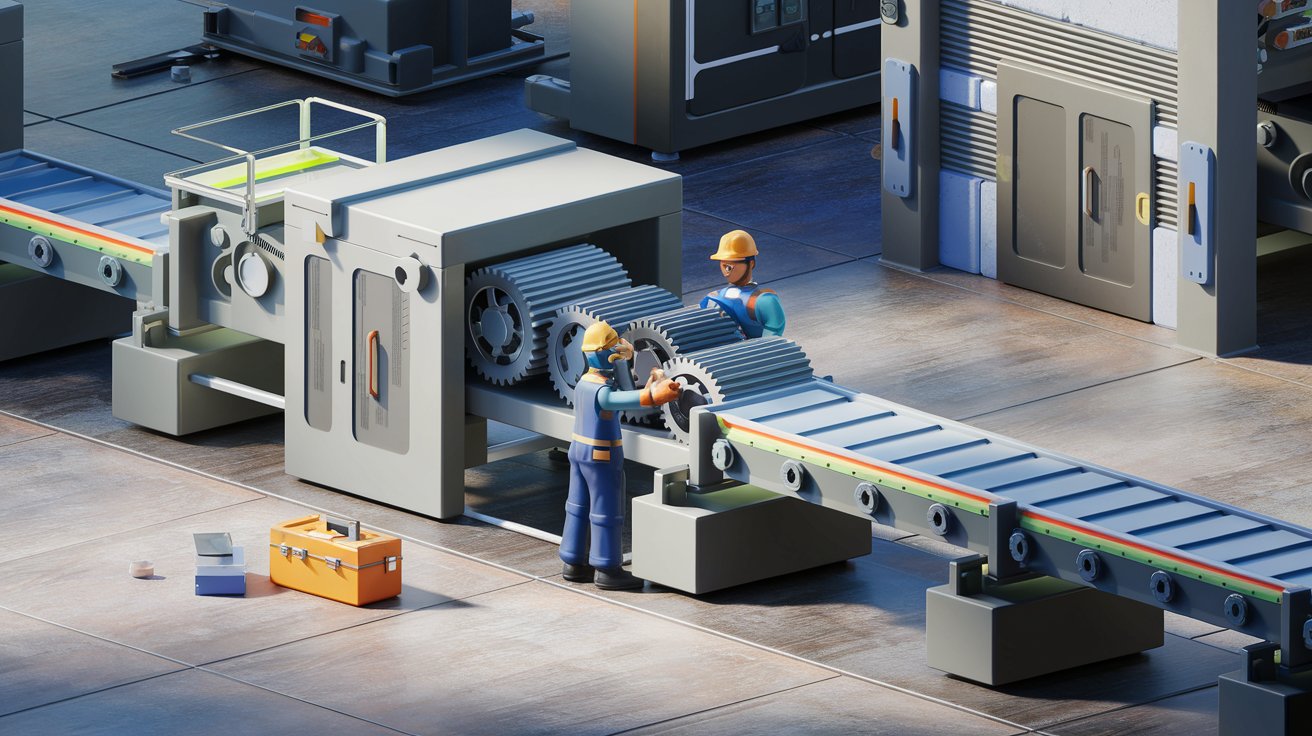
PM is a simple analogy of preventing breakdowns and delays through regular maintenance. It has been in play even before coining the name.
Some even call it a maintenance type that follows ‘Defective Attention’. Due to this effectiveness, preventive maintenance dominated most industries until the 21st century and the Industrial Revolution 4.0.
Meaning and Definition
Preventive Maintenance (PM) involves performing regular, scheduled maintenance on equipment to prevent unexpected failures. The aim & objective of PM– issue found and assessed, and now take actions to solve and extend the machine’s lifespan.
By adhering to a routine maintenance schedule, PM aims to minimize the risk of breakdowns and ensure smooth, uninterrupted operations. For a better illustration, Siemens manufacturing company employs PM in its operations. They service their gas turbine service centers using PM strategies.
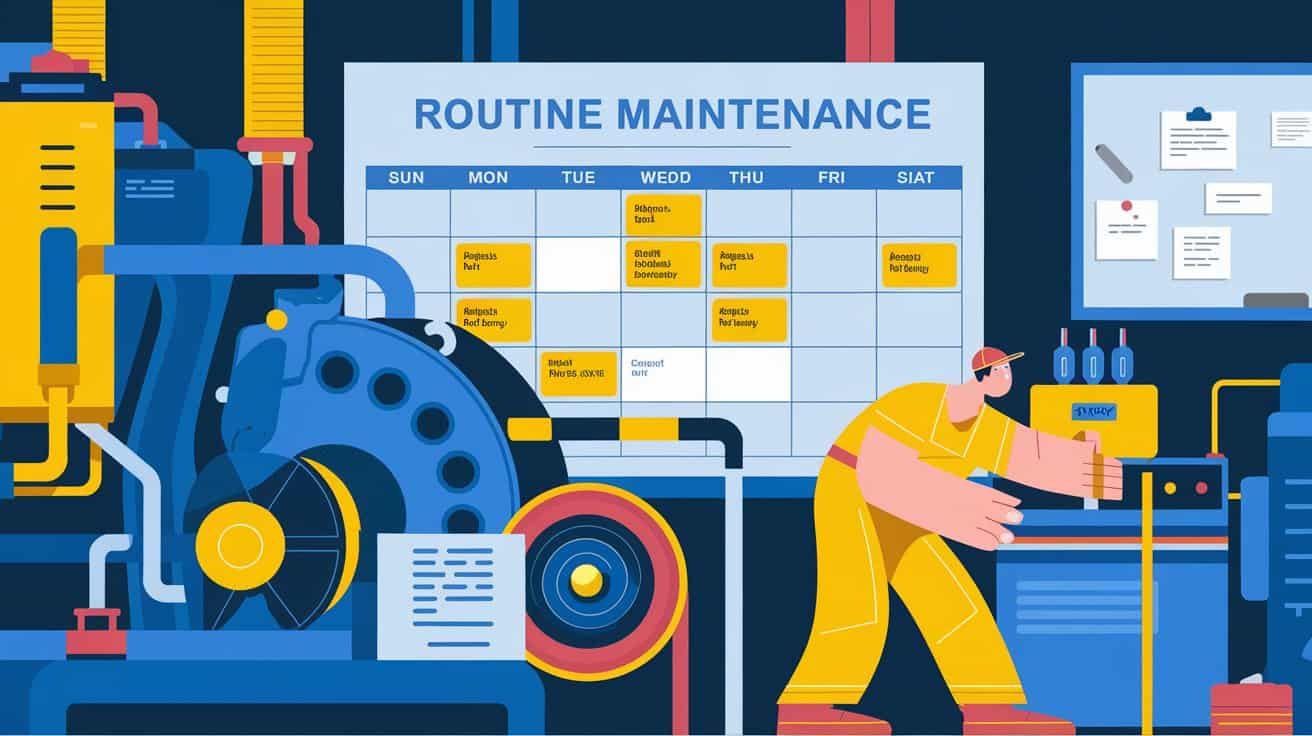
In one notable case, Siemens scheduled routine maintenance for a gas turbine used in a major power plant in Germany. By focusing on a preventive maintenance schedule, they were able to replace critical components before they showed signs of wear. This proactive approach helped avoid unexpected failures, ensured continuous operation, and significantly extended the turbine's operational life.
Even though PdM is the newly accepted maintenance type, global manufacturing companies still continue on PM.
Predictive Maintenance vs Preventive Maintenance
Even though predictive maintenance is largely accepted nowadays over preventive maintenance, no one is throwing away one for another. To leverage PdM, you don’t have to discard Pm. Instead, both strategies are being used side-by-side to optimize maintenance practices. The key lies in understanding their respective areas of application and how extensively each is leveraged.
Predictive maintenance focuses on analyzing real-time data and predicting potential failures before they occur, offering a more targeted and efficient approach. Conversely, preventive maintenance involves scheduled maintenance activities designed to prevent issues before they arise, ensuring ongoing operational reliability.
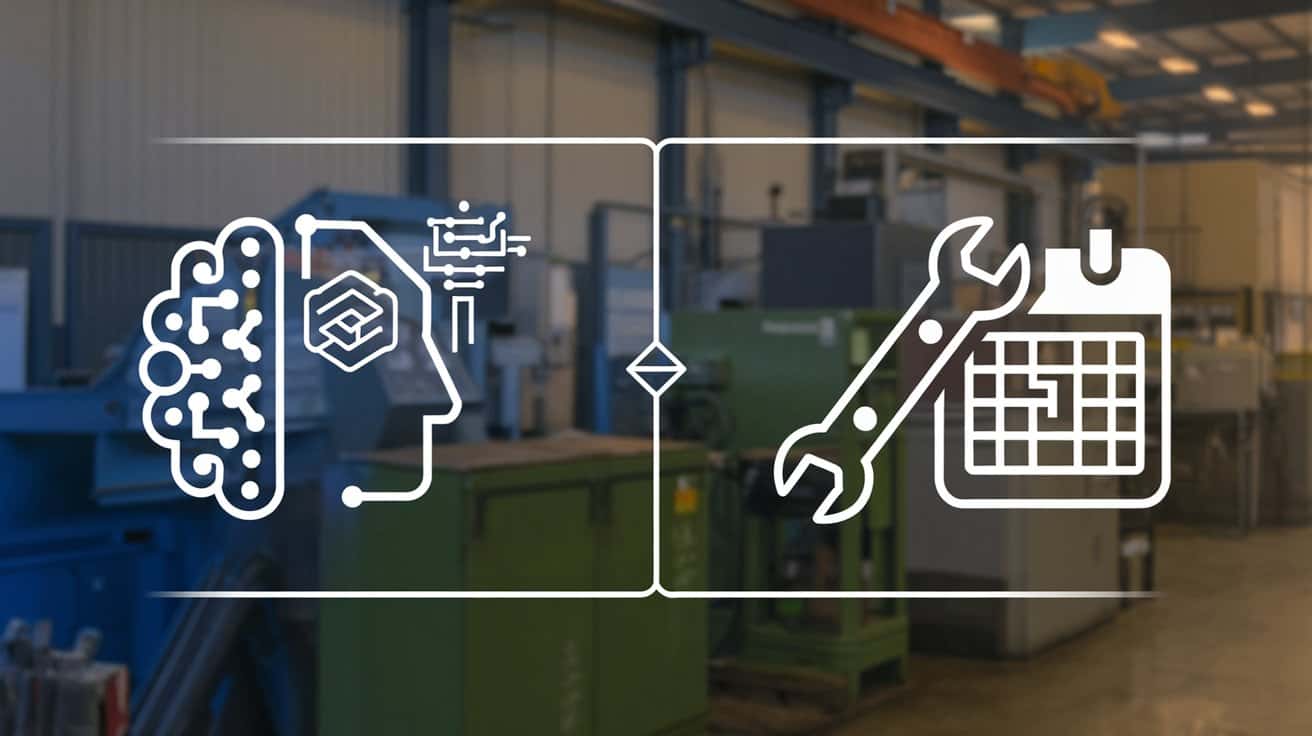
By integrating both methods, organizations can enhance their maintenance strategies. You need to balance between them to maximize the optimization of cost, time, and labor.
This combined approach is proven to lead to improved equipment performance and reduced downtime.
The Pros of Predictive Maintenance
- The best pro of Predictive maintenance is it detects issues even before taking place. The process uses data analysis to identify potential failures before they occur. Helps a lot in mitigating unplanned scenarios.
- Unlike preventive maintenance, PdM follows optimized maintenance scheduling. Maintenance activities are performed only when necessary.
- The procedure of maintenance saves money, wastes time, and labor.
- Real-time monitoring and data analysis enhance equipment performance and operational efficiency.
The Cons of Predictive Maintenance
- The initial cost to operate predictive maintenance is quite high. It requires investment in sensors, big data, data analytics tools, IoT, skilled personnel, and others.
- Collecting, handling, and analyzing large volumes of data is a tough task. Also, requires specific individuals of expertise.
- An effective PdM procedure relies on continuous data collection and analysis. Feasibility is a question here.
- Over-reliance has become a con for predictive maintenance in recent days. It leads to the possibility of overlooking other factors that could affect machine performance.
The Pros of Preventive Maintenance
- Regular maintenance is very common among companies and it’s a must. Preventive maintenance ensures that.
- Preventive maintenance is simple to implement and manage. Just involves some scheduled tasks rather than complex data analysis.
- Preventive maintenance ensures long-term repair and replacement cost reductions.
The Cons of Preventive Maintenance
- Over-maintenance is a possibility here. Preventive maintenance sometimes leads to unnecessary tasks even though do not require any intervention. It’s one of the biggest cons of this maintenance type that causes a huge time loss and waste of resources.
- Less responsive to emerging issues. Preventive maintenance routines do not address any unexpected intervals due to machine failure or any other causes.
- The schedule is fixed and pre-planned rather than depending on actual equipment condition.
Reactive vs Preventive vs Predictive Maintenance
Reactive maintenance is a ‘run-to-failure’ approach. This involves repairs and maintenance per occurrence.
Even though the initial cost is low the repair cost could be higher and also, cause a good amount of unplanned disruption time. So in short, it’s straightforward but can be costly and disruptive.
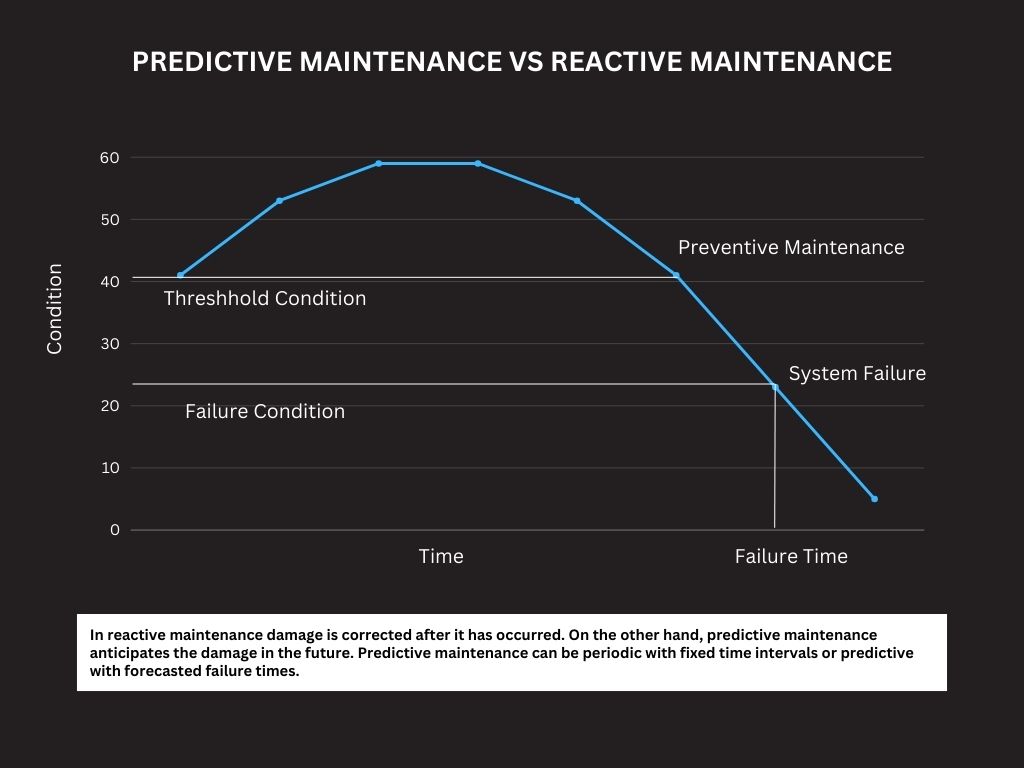
Based on different analyses and pros & cons, both preventive and predictive maintenance strategies can improve equipment reliability and reduce costs compared to reactive maintenance.
Corrective Maintenance
If we are to discuss Preventive vs Predictive vs Corrective Maintenance, corrective maintenance might turn out to be a better option in instant maintenance.
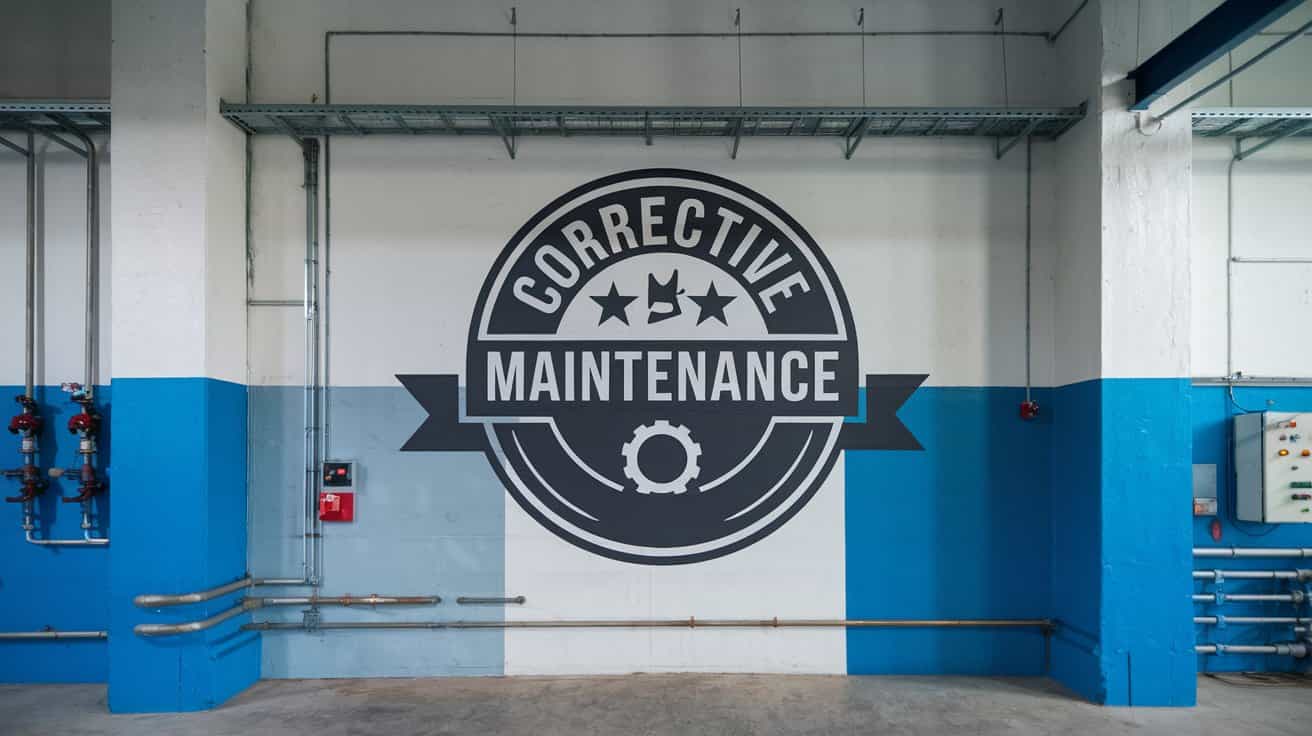
Corrective maintenance is a type of reactive maintenance. This maintenance type occurs after the machine fails. It involves repairing or restoring equipment to its normal operating condition following a breakdown.
This reactive approach addresses problems only after they arise. However, the downside is this often leads to unplanned downtime and potentially higher repair costs compared to PdM and Pm.
Bottom Line
The recent revolution of AI with the dawning of Industry 5.0 is going to further enhance these maintenance types, especially predictive maintenance. Already companies like Intel, Siemens, Martin Lockheed, Toyota, Apple, Ford, Boeing, and many others are leveraging this integration in equipment maintenance. Furthermore, they have seen significant optimization. So, the integration of AI is expected to refine further these maintenance strategies.
Both predictive and preventive maintenance strategies offer distinct advantages for optimizing equipment reliability and performance. While Predictive maintenance reduces potential downtime and maintenance costs– preventive maintenance provides prevention from unexpected breakdowns ensuring consistent operational efficiency.
Ultimately, the choice is not specific. A lot of factors come into play to decide predictive maintenance vs preventive maintenance. So the decision should be guided by your specific operational needs and goals.